Hydrodistillation is a traditional method for the extraction of bioactive compounds, mainly essential oils from plants. Solvents are not involved, and it can be performed before the dehydration of plant materials. Hydrodistillation involves three main physicochemical processes; hydrodiffusion, hydrolysis, and decomposition by heat. At a high extraction temperature, some volatile components may be lost. This drawback limits its use for thermo-labile compound extraction.
There are three types of hydrodistillation: water distillation, water-steam distillation, and steam distillation. In hydrodistillation, first, the plant material is packed into a still compartment, then water is added in sufficient amounts, and finally brought to boil. Alternatively, direct steam is injected into the plant material. Hot water and steam act as the main influential factors to free bioactive compounds of plant tissue. Indirect cooling by water condenses the vapor mixture of water and oil. Condensed mixture flows from the condenser to a separator, where oil and bioactive compounds separate automatically from the water.
The hydrodistillation process may generate large volumes of mother liquors. Besides the waste disposal problem, this liquor represents an additional added value because of its water-soluble phenolics. Rocha-Guzmán et al. (2007) reported that the ethyl acetate extract of the mother liquors obtained from the hydrodistillation of oregano could be superior to ascorbic acid and butyl hydroxyl toluene when used at high concentrations. Moreover, the solid residue of the hydrodistillation process is usually disposed of, although it is a rich source of antioxidant compounds. Treating the wet residual material (herb and water) remaining after the hydrodistillation process could lead to extracts rich in phenolic acids, taking full advantage of the process wastes.
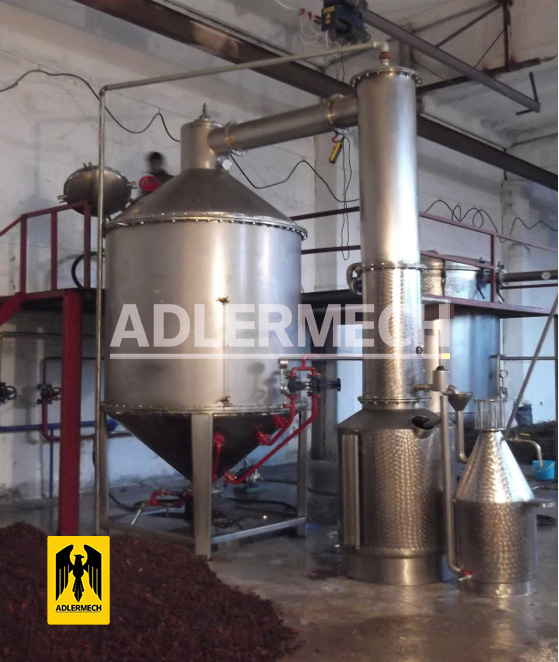
There are several different types of equipment that may be used in the production of hydrosols, including steam distillation systems, water distillation systems, and vapor pressure distillation systems. The specific type of equipment chosen will depend on the type of plant material being processed and the desired characteristics of the final product.
In a steam distillation system, the plant material is placed in a distillation vessel and steam is introduced into the vessel. The heat and steam cause the volatile oils and water-soluble compounds in the plant material to vaporize, and the vapors are then condensed and collected as hydrosol.
In a water distillation system, the plant material is placed in a distillation vessel along with water. The heat and steam produced by boiling the water cause the volatile oils and water-soluble compounds in the plant material to vaporize and the vapors are then condensed and collected as hydrosol.
In a vapor pressure distillation system, the plant material is placed in a distillation vessel and heated to a temperature at which the volatile oils and water-soluble compounds in the plant material vaporize. The vapors are then condensed and collected as hydrosol.
Hydrosol distillation equipment typically includes a distillation vessel, a condenser, and a collection vessel. The distillation vessel is used to hold the plant material and the condensing medium (steam or water), and the condenser is used to cool and condense the vapors produced during the distillation process. The collection vessel is used to collect the hydrosol as it is produced.